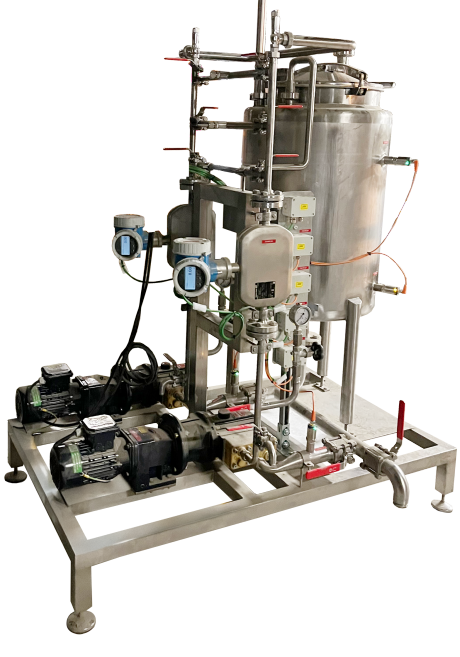
Unloading and precise additives injection before crushing
A complete additive management system, from unloading from the tanker into storage tanks precise and monitored additive injection.
A powerful Pompetravaini centrifugal pump ensures the unloading of the additive from a 30m3 tank into three interconnected storage tanks, which are monitored by radar sensors. From these large tanks, the additive is automatically filled into a small 200l tank of the dosing unit and then injected onto one or two production belts, along which the stony material moves into the mill. A constant and precise injection rate is monitored by a combination of a Wanner HydraCell-G dosing pump and mass flow meters. The correct injection rate ensures significant energy savings during the crushing process.
SYSTEM PARAMETERS
- Flow rate: 10 - 100 l/h
- Pressure: 2 bar
- Accuracy: 1-2%
- Medium: additives (glycol)
- Medium concentration: 100%
- Medium temperature: 5-40°C
- Viscosity: 1-100 cP
- Tank capacity: 200 l
- Height: 2 m
- Footprint: 1,8 x 1,8 m
- Weight: 200 kg
- Materials: Stainless steel 316L, brass
- Certifications: CE
Used components:
Wanner Hydra-Cell G
Pompetravaini TCH
Features:
- Fully automatic stock monitoring process on the ground floor
- Minimal maintenance thanks to sealless pump design
- Option to connect an additional IBC with experimental additive for property testing
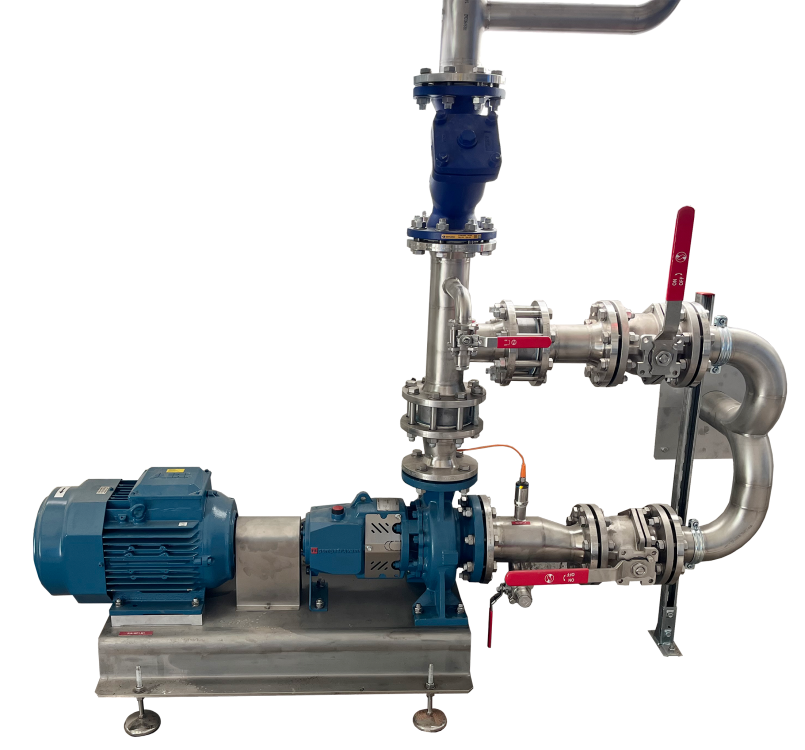